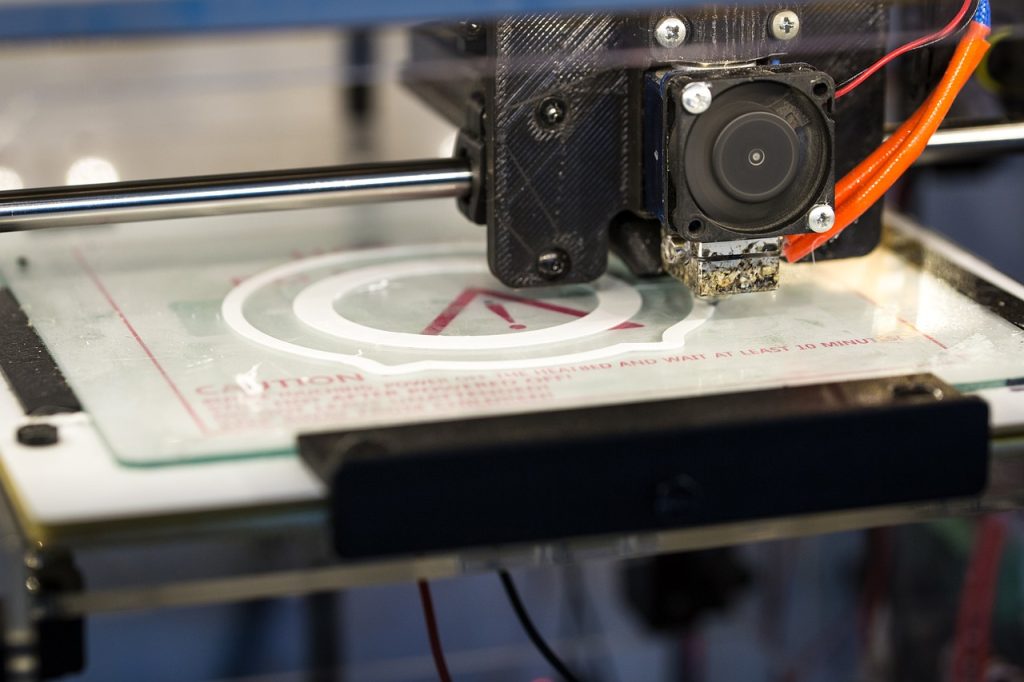
In the realm of manufacturing, the emergence of 3D printing has sparked a technological revolution that is reshaping industries and redefining what’s possible. This innovative additive manufacturing process has transcended traditional limitations, enabling companies to produce intricate, customized, and efficient components with unprecedented ease. In this blog, we will explore the groundbreaking applications of 3D printing in manufacturing, showcasing how this technology is changing the landscape of production and design.
- Rapid Prototyping and Iteration
One of the most significant advantages of 3D printing in manufacturing lies in its ability to expedite the prototyping phase. Traditional manufacturing methods often require time-consuming tooling and molds, which can delay product development. 3D printing enables manufacturers to create prototypes directly from digital designs, accelerating the iterative process and allowing for faster feedback and improvements.
- Complex Geometries and Lightweight Structures
Traditional manufacturing techniques can be limited when it comes to producing complex geometries or lightweight structures. 3D printing overcomes these limitations by layering materials in a controlled manner, allowing for intricate designs that were previously unattainable. This is particularly valuable in industries like aerospace, where lightweight yet robust components are crucial for fuel efficiency and performance.
- Customization and Personalization
Mass customization is another revolutionary application of 3D printing in manufacturing. With the ability to produce individualized products economically, companies can cater to specific customer preferences without compromising efficiency. This capability extends to various industries, from fashion and jewelry to healthcare, where personalized prosthetics and implants can greatly enhance patient outcomes.
- Reduced Material Waste
Traditional manufacturing often generates significant material waste due to subtractive processes. 3D printing, on the other hand, is an additive process, meaning that material is only used where it’s needed. This reduction in material waste not only makes manufacturing more sustainable but also minimizes costs associated with raw materials.
- Supply Chain Disruption and On-Demand Production
3D printing has the potential to disrupt traditional supply chains by enabling on-demand production. Instead of manufacturing products in large quantities and storing them in warehouses, companies can produce items as needed. This “just-in-time” production reduces inventory costs and eliminates the need for excess storage space.
- Tooling and Jig Creation
Manufacturing often requires specialized tools, jigs, and fixtures to ensure accurate production. 3D printing can be used to rapidly produce these tools, reducing lead times and costs associated with traditional tooling methods. This is especially beneficial for small-batch production runs or instances where design changes are frequent.
- Prototyping and Testing Functional Parts
3D printing is not limited to creating prototypes; it can also produce functional parts that can be tested and evaluated under real-world conditions. This helps identify design flaws and areas for improvement before committing to full-scale production, ultimately saving time and resources.
Conclusion
The applications of 3D printing in manufacturing are nothing short of transformative. From revolutionizing prototyping to enabling intricate designs and personalized products, this technology is reshaping industries across the board. The ability to produce complex geometries, reduce waste, and create on-demand brings efficiency, customization, and sustainability to the forefront of manufacturing practices. As research and innovation continue to drive the evolution of 3D printing, we can only anticipate even more groundbreaking applications that will reshape the future of manufacturing as we know it.